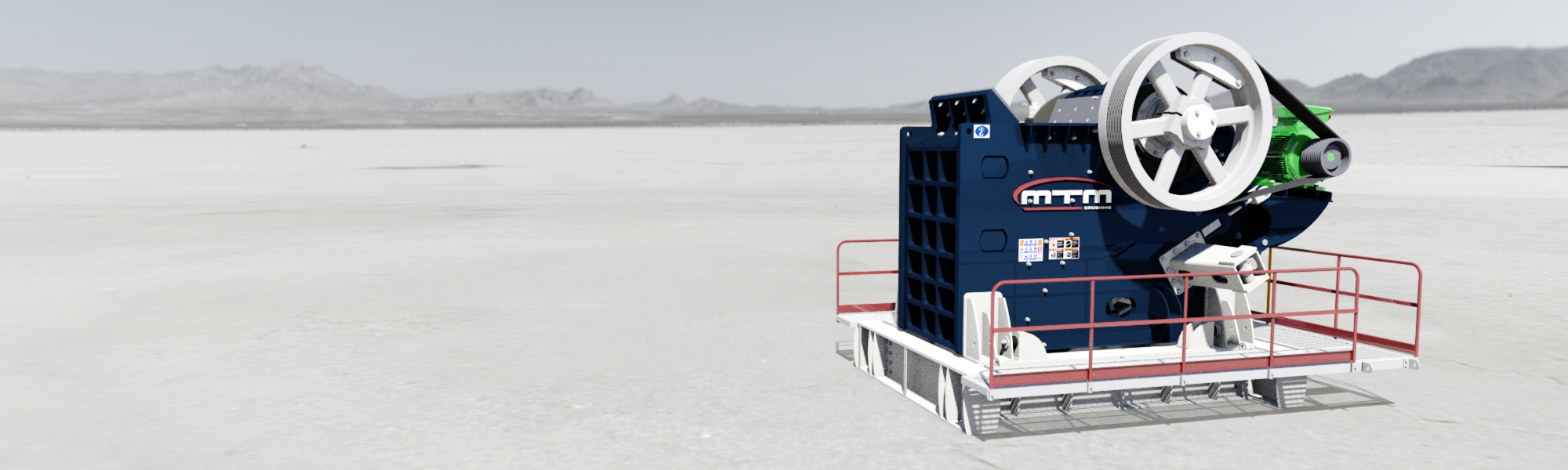
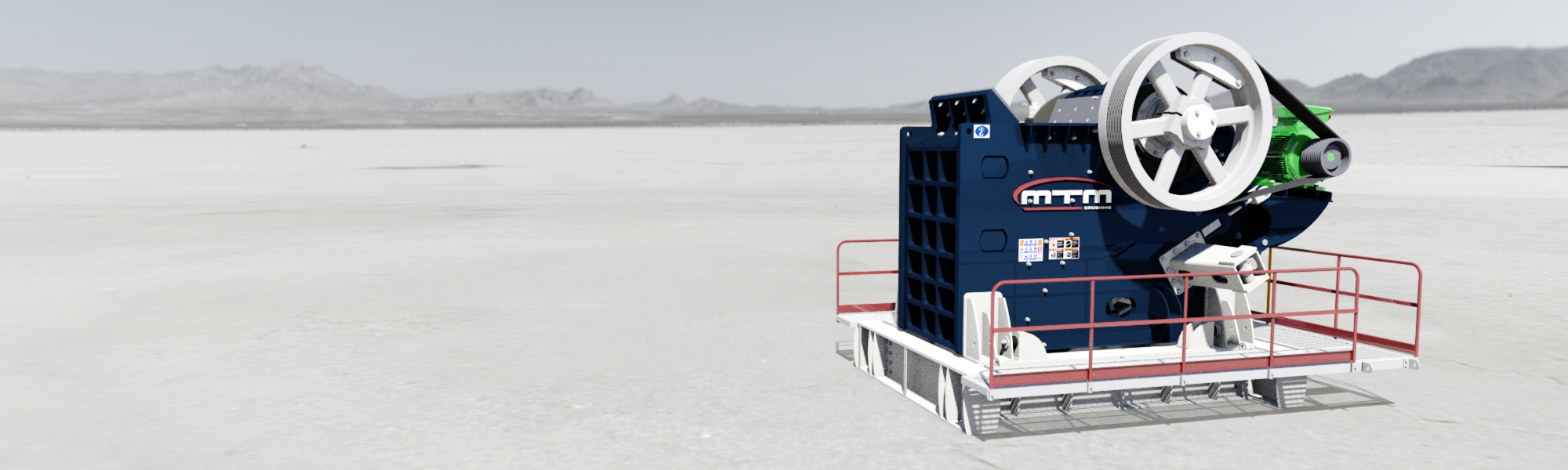
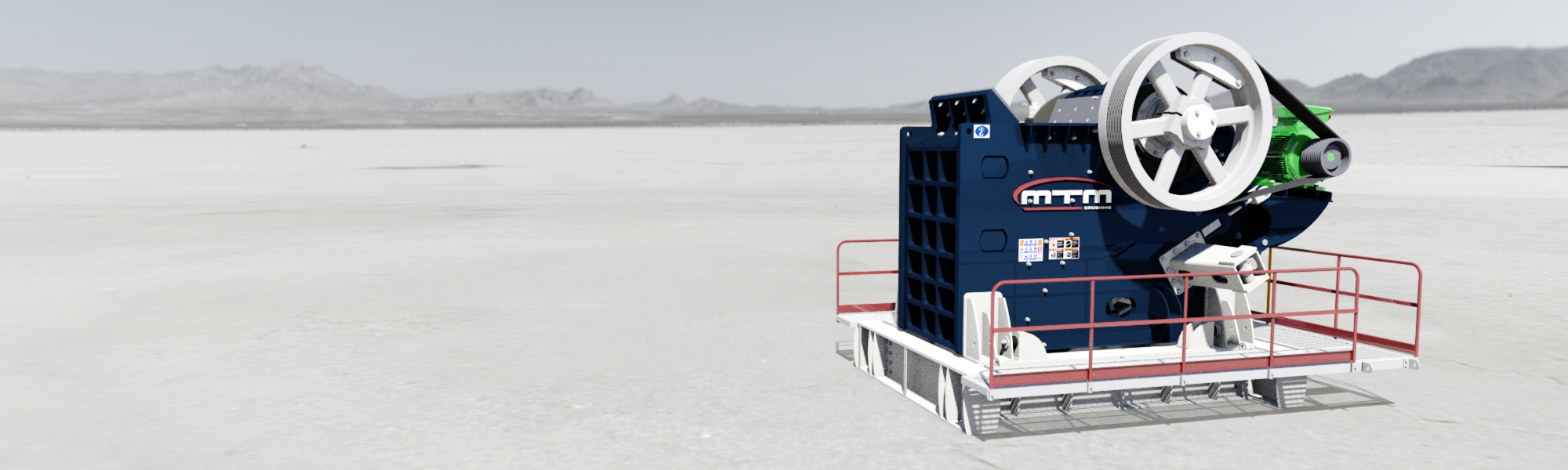
ÇENELİ KIRICILAR
Madencilik, kimyasal yapı malzemeleri, agrega üretimi gibi alanlarda hammaddelerin kullanılabilmeleri için ebatlarının uygun ölçülere getirilmesi gereklidir. Dünyada kullanılan hammadde ve malzemeler oldukça çeşitlidir. Malzemelerin kimyasal ve fiziksel özelliklerine bağlı olarak kırma işlemleri için seçilecek kırıcı tipleri de farklıdır.
Kırıcı seçimlerinde dikkat edilmesi ve mutlaka göz önünde bulundurulması gerekli kriterler genel olarak aşağıda verilmiştir;
1.Malzemelerin sertlik değeri
2.Kırılabilme mukavemeti
3.Malzemenin yoğunluğu (Yığın yoğunluğu ve Özgül ağırlığı)
4.Nem miktarı
5.Kırma Kapasitesi ihtiyacı (saat/gün/yıl)
6.Beslenen malzemenin ebatları, mümkünse beslenen malzeme istatistiksel dağılım ölçüleri ve yüzdeleri
7.Amaçlanan ürünün ebatları, mümkünse istenen istatistiksel dağılım ölçüleri ve yüzdeleri
8.Ürün için hedeflenen şekilsel özellikler (yassılık, kübiklik, kirlilik vb. özellikleri)
9. Malzemenin yanıcı, patlayıcı, aşındırıcı, yapışkan, elastik, kırılgan vb. özellikleri
Çeneli kırıcılar genellikle düşük devirli çalışan ve malzemelerin kabaca kırılması amacıyla kullanılan, baskı kuvveti uygulayarak boyut küçültme işlemi yapan kırma makinalarıdır. Beslenen malzemeler kırılabilmesi için hareket etmeyen sabit çene ile hareketli çene arasında sıkıştırılır.
Madencilik, inşaat ve yapı malzemeleri sektöründe kullanılan genel kırma kademeleri aşağıda açıklanmaktadır:
1.Kaba kırma (Primer Kırma) işlemi sonrasında malzemeler 125-250 mm aralığına getirilir. Genellikle çeneli kırıcıların birinci aşamada kullanıldığı sistemlerde beslenen malzemelerin maksimum büyüklüğü 1000 mm olarak alınabilir.
2.Sekonder kırma işleminden geçen malzemeler 0-50 mm aralığına indirilir. Beslenecek malzemelerin maksimum büyüklüğü 250-500 mm olarak bu aşamada kabul edilebilir.
3.Tersiyer (İnce) kırma işleminde ise malzemeler 0-25 mm ölçülerine getirilir ve bu grupta yer alan kırıcıların alabileceği maksimum ebatlar 25-150 mm olarak kabul edilir.
4.Mikronize kırma aşamasında ise malzemeler 0-1000 mikron ölçülerine indirilir. Beslenecek malzemelerin ise kırıcı tasarımına bağlı olmakla birlikte maksimum 25 mm olarak düşünülebilir.
Kırma aşamalarına ve malzeme özelliklerine göre kırıcı seçimleri uzman personel tarafından yapılmalıdır. Özellikle sekonder kırma aşamasında kullanılan çeneli kırıcılar için geri dönüş yükleri çok dikkatli bir şekilde planlanmalıdır. Aksi halde sekonder çeneli kırıcı performansı beklenen seviyelerden düşük olacaktır.
Bir çeneli kırıcı en basit haliyle ana taşıyıcı gövde üzerinde dik olarak konumlandırılmış iki adet kırıcı çene yüzeyinden oluşmaktadır. Bu kırıcı çenelerden bir tanesini sabit olarak durur iken, diğeri ise hareket merkezi etrafında belli bir yörüngede hareket etmektedir. Kırıcıya beslenen iri malzemeler bu iki çene arasında sıkıştırma kuvveti sayesinde kırılarak hareketli çene ve yerçekimi sayesinde kırıcının aşağı tarafından boşaltılmaktadır. Kırıcıya beslenen iri malzemeler kırıcının çıkış bölgesinin besleme bölgesine göre ebatlarının daha küçük olması sayesinde ebat olarak indirgenerek kırıcıdan dışarı alınmaktadır. Çeneli kırıcıların kırma verimleri genel olarak bu küçültme miktarına göre değerlendirilir. Bu oran tasarımdan tasarıma değişmekle birlikte ortalama 3 veya 7 kat indirgeme oranı şeklinde kabul edilebilir. Kırıcılarda indirgeme oranları farklı yöntemlerle hesaplanabilir, ancak en çok kabul gören indirgeme oranı aşağıdaki şekilde hesaplanır;
İndirgeme Oranı (%80 Geçen Miktara Göre)=Kırıcıya Beslenen Malzemelerin %80 inin Geçtiği Elek ölçüsü (mm)-F / Kırıcı Çıkışından alınan malzemelerin %80 inin geçtiği elek göz ölçüsü(mm)-P
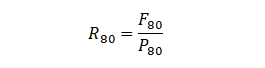
İndirgeme oranları için farklı kabullerle değişik şekillerde hesaplamalar da yapılabilir, aşağıda bazı örnek indirgeme oranları verilmiştir.
İndirgeme Oranı (Ortalama Malzeme Büyüklüğüne Göre)=Kırıcıya Beslenen Malzemelerin ortalama ölçüsü(mm)-F / Kırıcı Çıkışından alınan malzemelerin ortalama ölçüsü(mm)
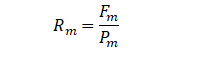

Görünen İndirgeme Oranı=Kırıcı Çene Ağzı Genişliği-W / Kırıcı Çıkışı Ayarının Kapalı Konumu-CSS
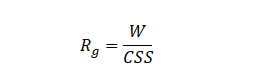
ÇENELİ KIRICI ÇEŞİTLERİ
Çeneli kırıcılar tasarım özelliklerine göre üç ana sınıfta değerlendirilebilir;
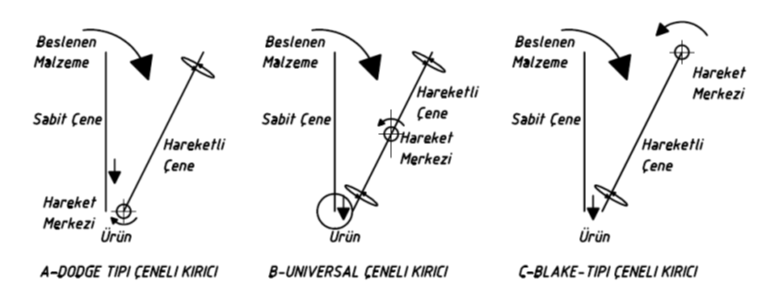
A.Hareket Merkezi Aşağıda Olan Çeneli Kırıcılar (Dodge Tipi)
Bu tip kırıcılarda hareket merkezi ana gövde yapısının aşağısında bulunmaktadır. Hareketli çene kırıcının besleme tarafında en yüksek hareketini yapar ve besleme bölgesinin ölçüleri bu sayede belli aralıkta değişkenlik gösterir. Kırıcın çıkış ağzı sabit aralıktadır ve ayar yapılamaz. Bu nedenle istenen ürün ebatlarının kesin ve değişmez nitelikte olması gereklidir. Kırma verimleri yüksek olmasına karşın kapasiteleri günümüz ihtiyaçlarına cevap veremeyecek kadar düşüktür. Ayrıca beslenen malzemenin çıkış ağzı ölçülerinde olma zorunluluğu kırıcının çabuk boğulmasına veya tıkanmasına neden olur. Bu özellikleri nedeniyle çok yaygın bir kullanım alanı bulamamıştır. Küçük kapasiteli kırma ihtiyaçları için laboratuvarlarda veya numune hazırlama işlemlerinde kullanılabilirler.
B. Hareket Merkezi Ortada Olan Çeneli Kırıcılar (Universal Tip)
Bu kırıcılarda hareket merkezi ortada olduğundan hareketli çenenin kırma hareketi hem besleme tarafında hem de çıkış tarafında çalışma sırasında hareketli ve değişkendir. Bu tip kırıcılar günümüzde kullanılmamaktadır. O nedenle bu yazıda daha fazla üzerinde durulmayacaktır.
C.Hareket Merkezi Yukarıda Olan Çeneli kırıcılar (Blake Tipi)
İlk olarak Eli Blake tarafından 19.Yüzyılın ikinci yarısında yol yapımında kullanılacak olan malzemeleri üretebilmek için icat edilmiştir. O yüzden bu tip çeneli kırıcılar Blake-Tipi kırıcılar olarak da anılmaktadır. Başlangıçta kapasiteleri oldukça düşük olmasına karşın, ilerleyen dönemlerde kırıcı gövdelerinin büyütülmesiyle birlikte günümüzde kapasiteleri 0-300 mm ürün alınabilecek şekilde 1000 ton/saate kadar çıkabilmektedir. Mevcut bir çeneli kırıcının alt çıkış aralığı arttıkça kapasitesi e doğrusal olarak artar. Alt çıkış aralığı kırıcının her bir devri için kırıcı tasarımına bağlı olarak minimum (CSS) ve maximum (OSS) değerler arasında hareket eder. Bu aralık değerine “Throw” adı verilir. Karşılığı “Hareket Miktarı” olarak dilimize çevrilebilir ve çeneli kırıcı çıkışı makinanın çalışması sırasında bu iki aralık arasında gider ve gelir.
1.Minimum Çene Açıklığı (CSS-mm)
2.Maksimum Çene Açıklığı (OSS-mm)
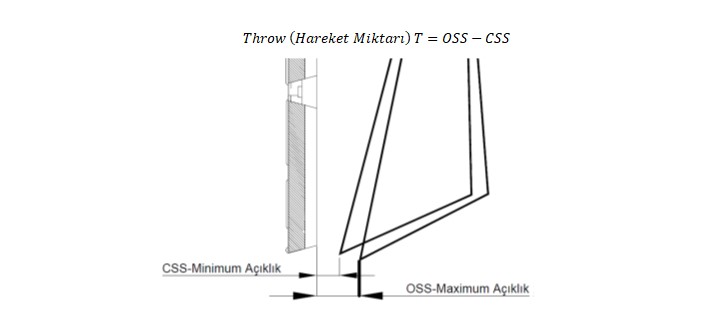
BLAKE Tipi kırıcıları iki gruba ayırabiliriz;
1.Çift Emniyet Plakalı Çeneli Kırıcılar
Tasarım itibariyle kırıcıdan elde edilen baskı kuvvetini daha da arttırabilmek amacıyla çift emniyet plakalı olacak şekilde tasarlanmış hareket merkezinin yine yukarıda olduğu ağır hizmet tipi çeneli kırıcılardır. Kırılma mukavemeti, aşındırıcılığı ve sertlik değeri (Moh’s Sertliği> 7 ) oldukça yüksek olan kayaçların kırılması için uygundurlar.
1.Tek Emniyet Plakalı Çeneli Kırıcılar
Adından da anlaşılabileceği üzere tasarımında tek emniyet plakasının kullanıldığı çeneli kırıcılardır. Hareket merkezinin yukarıda olması nedeniyle Pitman grubunun hareketi yukarıdan aşağıya inildikçe artar ve en alt noktada maksimum değerine ulaşır. Yerçekimi ve ovalama hareketi sayesinde tıkanma özelliği çok düşüktür. Yüksek kapasitelerde üretim için daha uygundur. Bakım ihtiyacı düşük ve kolaydır. Bu avantajlarından dolayı da dünya üzerinde en fazla üretilen ve yaygın olarak kullanılan çeneli kırıcı tipidir. Bu yazıda bu tipteki kırıcılar hakkında daha detaylı bilgi verilecektir. Ancak kırıcının mekanik veya geometrik analiz detaylarına girilmeyecek tecrübelere dayalı bazı başparmak kurallarından kısaca bahsedilecektir.
Tek Emniyet Plakalı Çeneli Kırıcıların Çalışma Prensibi;
Bu tip bir kırıcının ana çalışma prensibi aslen mekanizmalar literatüründe bahsi geçen dört kol mekanizmasının bir uygulamasıdır. Bu tipteki kırıcıların mekanizma karşılığı aşağıda şematik olarak verilmiştir.
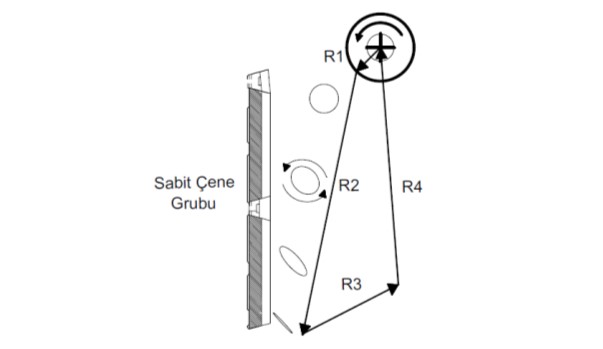
R1 Kolu: Mil eksantrikliği
R2 Kolu: Hareketli Çene (Pitman ) Grubu
R3 Kolu: Mesnet Plakası
R4 Kolu : Ayar Bloğu ve Mil Merkezi Arası
Hareket merkezini Pitman grubundaki eksantrik mil merkezi oluşturur. Ana gövde yan yataklarına merkezlenmiş olan mil volandan almış olduğu hareketi eksantrik olması sayesinde hareketli çene (Pitman) grubuna iletir. Hareketli çene grubu yukarıda verilen şematik dört kol mekanizmasının fiziksel parametrelerine uygun olarak eksantrik mil merkezinden uzaklaştıkça farklı yörüngeler izleyerek hareket eder ve beslenen malzemeye çalışma periyodunun yaklaşık yarısı kadar süre içinde güçlü bir baskı ve ovalama kuvveti uygular. Geri kalan diğer yarım sürede ise hareketli çene (Pitman) grubu geri çekilme hareketi yaparak malzemelerin aşağıya inmesine zaman tanır. Bu döngü malzeme kırılıp çıkış bölgesine gelene kadar devam eder.
Pitman grubunun yapmış olduğu hareket besleme bölgesinde dairesel bir yörünge çizerken, aşağıya doğru ilerledikçe eliptik ve en alt noktada ise neredeyse doğrusal bir yörünge izlemektedir. Beslenen malzemeler yerçekimi ve ovalama hareketi sayesinde kırılıp ufaltılarak kırıcıdan tahliye edilir.
Aşağıda tek emniyet plakalı çeneli kırıcı tasarımına ait örnek bir kesit verilmiştir.
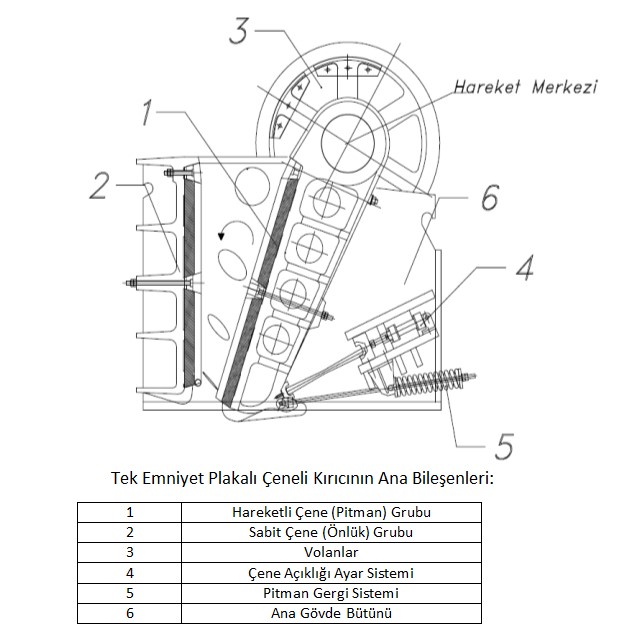
1-Hareketli Çene (Pitman) Grubu:
Çeneli kırıcılarda kırma işlemini yapan kırıcının tahrik sistemi olarak da adlandırılan hareketli parçalardan oluşan gruptur.
Pitman, hareketli çene ve sıkma kamaları, rulmanlar ve eksantrik milden oluşur.
Hareketli Çene (Pitman) : Tamamen tek parça çelik dökümden üretilen ve üzerinde değiştirilebilir kırıcı çene bulunan parçadır. Motordan volan ve mil sayesinde almış olduğu güç ile kompleks bir yörünge izleyerek beslenen malzemeyi kendi gövdesi ile sabit çene arasına sıkıştırarak kırma görevini yerine getirir. Malzeme olarak yüksek dayanımlı çelik kullanılır. Kırıcı büyüklüğüne bağlı olarak 1-15 ton aralığında tek parça olarak üretilebilir.
Geometrik şekil itibariyle eksantrik mil merkezinden uzaklaştıkça kesitinin incelmesi hareket kolaylığı açısından tercih edilmelidir.
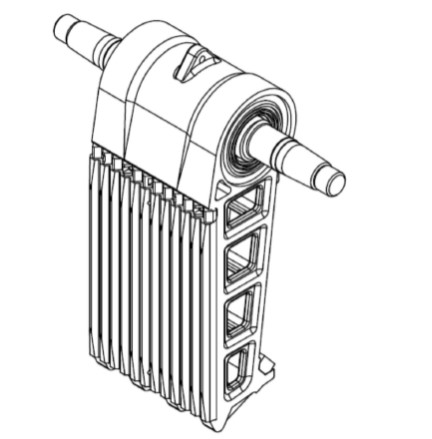
Eksantrik Mil:
Hareketli Çeneye (Pitman) volandan aldığı dönüş hareketini iletir, iki adet oynak makaralı rulman ile Pitmana iki adet oynak makaralı rulman ile de ana kırıcı gövdesine yataklanır. Her iki ucunda da birer adet volan bulunur. Günümüzde üretilen çeneli kırıcılarda mil malzemesi olarak yüksek mukavemetli çelik tercih edilir. (DIN-17200 /AISI 4140/ C4140 …).
Genel olarak eksantriklik değerleri 10-30 mm aralığında seçilir. Eksantriklik miktarı arttıkça Pitman grubunun hareketi de artar, ancak kırıcının güç ihtiyacının da artacağı ve daha büyük motor kullanılması gerektiği unutulmamalıdır.
Oynak Makaralı Rulmanlar:
Çeneli kırıcıların tahrik sisteminde iki farklı ebatta toplam dört adet çift sıralı oynak makaralı rulman kullanılır. Pitman için kullanılan rulmanlar çap olarak daha büyüktür. Kırıcı ebatları büyüdükçe montaj-demontaj ve bakım kolaylığı için manşon kullanılması tavsiye edilir.
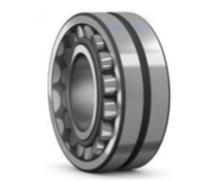
Labirentler:
Rulmanların uzun ömürlü çalışmalarını sağlamak ve yağlama işlemlerine yardımcı olmak açısından amacıyla labirent adı verilen sabit veya dönen sızdırmazlık bileşenleri kullanılmaktadır. İstisnai yataklama sistemleri haricinde genelde her bir takım labirent sistemi birbirine uyumlu iki parçadan oluşur, biri sabit halde dururken diğeri mekanizmanın hareketine uyum sağlamaktadır. Yukarıda verilen tahrik kesitinde rulmanların her iki tarafında yer alan labirentler de görülmektedir. Pitman içindeki rulmanların arka tarafında bir adet labirent bulunur, gres tutucu olarak ta adlandırılan bu parça aşırı gresin pitman içindeki mil boşluğuna geçmesine engel olur, rulmanların pitman içi hizalanmasını sağlar, ayrıca bu rulmanlar için gres rezervuarı işlevini görür.
2. Sabit Çene (Önlük) Grubu:
Ana kırıcı gövdesine kaynaklı veya cıvatalı olarak monte edilen hareketli çene grubunun karşısına dik veya açılı olarak konan ana parçalardandır. Üzerinde değişebilir sabit çene plakasını taşır. Malzemeyi hareketli çene birlikte sıkıştırma görevini üstlenir. Genel olarak çelik döküm malzemeden üretilmesi tercih edilir. Oldukça büyük kırma kuvvetlerine dayanabilmesi gerekir. Hareketli çeneyle birlikte duruş pozisyonu kritik kavrama açısını oluşturur.
3. Volanlar:
Çeneli kırıcılarda eksantrik milin uçlarında iki adet volan yer alır. Volanlardan biri düz diğeri kanallı olarak üretilir. İstenirse her ikisi de kanallı yapılabilir.
Motordan alınan hareket kayışlar ve kanallı volan sayesinde eksantrik mile oradan da hareketli çene (Pitman) grubuna iletilir. Volanlar çeneli kırıcılarda hareket iletilmesin sağlamalarıyla birlikte iki farklı işleve daha sahiptir;
1.Sabit hız ve sabit tork üreten elektrik motorunu dengelemek;
Çeneli kırıcılar hareket döngüsü içinde yarı-zamanda kırılacak malzemeye baskı kuvveti uygularken maximum güce ihtiyaç duyar geri kalan zamanda geriye doğru çekilerek malzemenin aşağıya ilerlemesine olanak verir. Bu geri çekilme sırasında güç ihtiyacı minimuma iner. Volan bu güç değişkenliğini en aza indirerek güç kaynağının ürettiği kinetik enerji olarak depolar. Bu şekilde güç kaynağını dengelemiş olur.
2.Enerji depolamak ve sisteme kullanılması için geri vermek
Hareketli çene (Pitman) Grubu malzemeye kırma esnasında baskı kuvveti uygularken maximum güce ihtiyaç duyar ve motordan gelen güç ile volanda depolanan enerjiyi birlikte kullanabilir veya boşta olduğunda ise motordan alınan güç kinetik enerji olarak volanlar da depolanır.
Volandaki enerjinin ihtiyaç duyulduğunda kullanıldığında volan dönüş hızı yavaşlamaya başlar, enerji depolandığında ise artar.
Volanlarda depolanan kinetik enerji:
𝑬𝒌=𝟏𝟐.𝑰.𝝎𝟐; 𝑰=𝒎.𝒌𝟐
𝐼:𝑉𝑜𝑙𝑎𝑛𝚤𝑛 𝑎𝑡𝑎𝑙𝑒𝑡 𝑚𝑜𝑚𝑒𝑛𝑡𝑖-kgm2
𝜔:𝐴ç𝚤𝑠𝑎𝑙 𝐻𝚤𝑧−𝑟𝑎𝑑𝑠=𝜋.𝑛30
𝑚:𝑉𝑜𝑙𝑎𝑛𝚤𝑛 𝑎ğ𝚤𝑟𝑙𝚤ğ𝚤−𝑘𝑔
𝑘:𝐴𝑡𝑎𝑙𝑒𝑡 𝑌𝑎𝑟𝚤ç𝑎𝑝𝚤−𝑚
4. Çene Açıklığı Ayar Sistemi:
Ayar bloğu olarak da adlandırılır, kırıcı gövdesine kaynaklı veya cıvatalı olarak tespit edilen bu sistem sayesinde çeneli kırıcının çıkış aralıkları ayarlanabilir. Ayar bloğu ile hareketli çene grubu arasında emniyet plakası bulunur. Ayar yapılırken emniyet plakası (R4 Kolu) bu blok sayesinde ileriye veya geriye alınır. Büyük kırıcılarda ayar yapabilmek için hidrolik pistonlar kullanılması gereklidir. Piyasada ayar sistemleri için üreticiler birbirinden farklı yöntemler kullanabilir. Hepsinin amacı kırıcının çalışma sırasında hangi çıkış aralığında çalışacağını belirlemektir. Çıkış ayarını yaptıktan sonra sabitlemek amacıyla ayar plakaları, mekanik kama sistemi veya tamamen hidrolik sistemler kullanılabilir.
Emniyet Plakası pek öyle görünmese de kırıcının önemli parçalarındadır. Hem kırıcı mekanizmanın kollarından birini oluşturur hem de kırıcıya giren kırılamayacak parçalar geldiğinde en zayıf halka olması nedeniyle kırılarak makinanın büyük hasarlar görmesine engel olur.
5. Hareketli Çene (Pitman) Grubu Gergi Sistemi:
Çeneli kırıcıların çalışması sırasında hareketli çene grubunun mekanizmadan ayrılmaması için geriye doğru belirli bir kuvvet uygulamak gereklidir. Çünkü Hareketli çene grubu ile ayar bloğu arasındaki emniyet plakası herhangi bir yöntemle sabitlenmemiştir. Çeneli kırıcı çalışmıyor iken yerçekimi sayesinde ayar bloğu ile hareketli çene grubu (Pitman) grubu arasında sıkıştırılmıştır. Çalışma sırasında pitman grubunun ileri hareketinden dolayı emniyet plakası aşağıya düşecektir.
Gergi sistemleri de farklılıklar gösterebilir. Günümüzde kullanılan çeneli kırıcılarda, kırıcı büyüklüğüne bağlı olarak bir veya iki yaylı gergi mekanizması kullanılır. Ayrıca yine hidrolik pistonların kullanıldığı sistemler de mevcuttur.
6. Ana Kırıcı Gövdesi:
Yukarıda açıklamaya çalıştığımız tüm parçaları bir araya getiren çelik konstrüksiyon yapıdır. Kalınlığı kırıcı büyüklüğüne göre değişen iki ana plakadan ve destek parçalarından oluşturulur ve üzerine kırıcının tüm parçaları kaynaklı veya cıvatalı olarak monte edilir.
Ana gövde, sabit çene grubu ve hareketli çene grubuyla birlikte kırıcının kırma haznesini oluşturur. Aşınmalara karşı korunması için döküm veya aşınmaya dayanıklı sac malzemeden üretilen değişebilir yan astar plakalarıyla desteklenir.
Kırma kuvvetlerine dayanması ve uzun ömürlü olması açısından mutlaka sağlam bir yapıda üretilmesi gereklidir. Hata yapılması durumunda kırıcı kısa sürede dağılır ve yatırım boşa gider.
Çeneli Kırıcılar için kullanılan bazı terimler ve açıklamaları:
Çene Ağız Açıklığı: Çeneli kırıcıların tasarımı sırasında üretici tarafından belirlenen ve beslenen malzemelerin maksimum ölçülerini de sınırlayan önemli iki adet ölçüden oluşur;
Uzunluk: Çeneli kırıcı gövdesindeki karşılıklı yan plakalar arasındaki ölçü.
Genişlik: Gövdenin en üst noktasındaki sabit çene ve hareketli çene arasındaki ölçüdür.
Örnek: 110 luk Çeneli Kırıcı olarak piyasada bilinen çeneli kırıcıların yan gövde plakaları arası 1100 mm dir. Bu kırıcının üst bölgesinde çeneler arasındaki genişlik ise yaklaşık olarak 850 mm dir.
Maksimum Besleme Büyüklüğü:
Çeneli Kırıcılarda ağız açıklığının genişlik değerinin %80-85 ine karşılık gelen ölçüdür.
Çeneli kırıcıların maksimum besleme boyutu ağız açıklığı ölçülerinden genişlik değerinin % 80-85 oranını geçmemelidir. Yani 110 luk olarak anılan çeneli kırıcının verimli olarak çalıştırılabilmesi için beslenen malzemenin en büyük boyutu:
850mm*0,85 ~ 720 mm
Ölçüsünden büyük olmamalıdır. Aksi halde çeneli kırıcının sık sık tıkanma riski ortaya çıkacak ve tıkanmaları giderebilmek için zaman harcanacaktır.
Kavrama Açısı:
Sabit Çene Grubu ile Hareketli Çene (Pitman) grubu arasındaki açıdır.
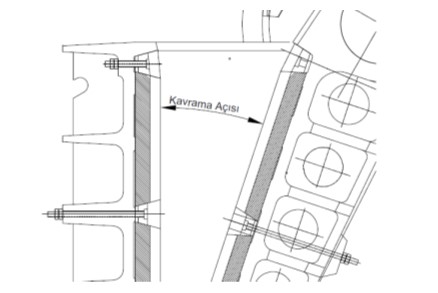
Kavrama açısı çeneli kırıcıların en önemli performans göstergelerinden biridir. Dünyada genel olarak kırılan kayaçların çelik ile olan ortalama sürtünme katsayısına dayanır ve 27 ° den daha büyük açılar tercih edilmez. Bu limit sürtünme katsayısı 0.5 değerine karşılık gelmektedir.
Bu değerden daha yüksek olan açıların kullanılması çeneli kırıcılarda malzemenin iki çene arasında kavranmasını oldukça güçleştirir ve kırıcı kapasitesinin düşmesine açar.
Kırıcı Çene Profilleri: Kırıcılarda kullanılan çeneler farklı profil tasarımlarına sahip olabilir. En yaygın olarak kullanılan profil tipleri oluklu, testere dişli veya düz profil olarak adlandırılan tiplerdir. Araştırma ve tecrübelere dayalı olarak çok farklı profiller geliştirmek mümkündür. Hangi uygulamada veya kırma aşamasında hangi profil tasarımının seçileceğine dair açık ve kesin kurallar yoktur. Ancak aşındırıcı malzemeler ve madencilik sektöründeki kırıcılarda düz profil tercih edilirken, asfalt ve beton agregası üretiminde oluklu tip profiller çeneler daha yaygın olarak kullanılmaktadır.
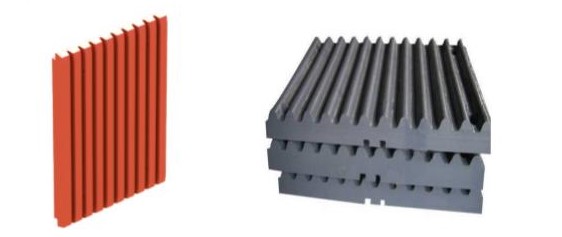
Malzeme olarak çeneler için en çok tercih edilen Yüksek Manganlı çelik (Hadfield Çeliği) dökümdür (%12-14, %16-18, %19-21 Mn). Ayrıca analiz olarak Cr, Mo, V, Ni gibi ilave elementler de aşınma dayanımlarını arttırabilmek için kullanılmaktadır. Ancak unutulmamalıdır ki fazladan ilave edilen sertlik ve aşınma dayanımını arttırmayı amaç edinen uygulamalar çenelerin normal kullanım ömrünü tamamlamadan kırılmalarına neden olabilir.
Kalker ve kireçtaşı için manganlı dökümlerde ortalama aşınma miktarı 25-50 gr/ton olarak düşünülebilir. Yüksek aşındırıcılığı olan malzemelerde bu miktar 500 gr/ton a kadar ulaşabilir.
Çenelerden en fazla faydayı sağlayabilmek için;
1.Çene profil yüksekliğinin yarısı aşınana kadar kullanılmalıdır.
2.Daha sonra ters çevrilerek profilin tamamı bitene kadar çalışılmalıdır
3.Tekrar ters çevrilerek kalan profil yüksekliğinin tamamı kullanılmalıdır.
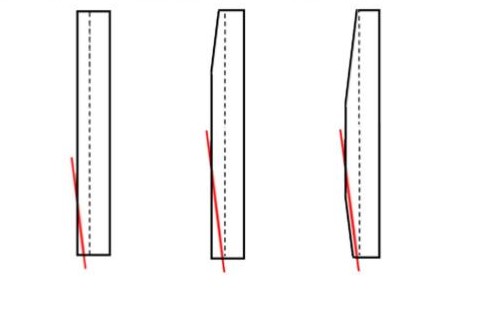
Çalışma Devri:
Çeneli kırıcıların çalışma devirleri Hareketli Çene (Pitman) Grubuna hareketi ileten volan ve eksantrik milin bir dakika içindeki dönüş sayısıdır. Genel olarak çeneli kırıcılarda yapı büyüklüğü arttıkça devir sayıları düşmektedir. Madencilik ve agrega sektörlerinde kullanılan çeneli kırıcılar genel olarak 200-350 devir/dakika aralığında çalışmaktadır. Makine imalatçıları tarafından tasarım parametrelerine göre belirlenmiş devirler makina için en uygun olan kritik devirlerdir. O yüzden çok iyi tasarlanmış çeneli kırıcılarda devir değişiklikleri tavsiye edilmez. Zorunlu ise mutlaka üreticisi veya bir uzman personele danışılmalıdır. Kırıcı devirleri hesaplanan kritik devir sayısına yakın değerlerde seçilmelidir. Çok düşük veya çok yüksek devirler çeneli kırıcıların performanslarını olumsuz yönde etkileyecektir.
Kritik devir sayısı:
Çeneli kırıcıların temel kapasitelerinin hacimsel olarak hesaplanması ve düşünülmesi gereklidir. Bu konuda literatürde farklı görüşler ve değişik hesaplama formülleri kullanılmaktadır. Bu yazımızda literatürdeki bazı hesaplama yöntemlerine değinilecektir. Ancak akılda tutulması gereken kırıcı kapasitesinin hacimsel büyüklük algılanması gerektiğinden malzemelerin yoğunlukları değiştikçe piyasada ton/saat olarak anılan kapasite değerlerinin de değişeceğidir.
Genelde makina üreticileri tarafından verilen tablolardaki çeneli kırıcıların kapasiteleri yığma yoğunluğu 1,6 ton/m3 olan malzemelere göre hesaplanmıştır. Aynı büyüklükteki kırıcı ile yığın yoğunluğu 1,0 ton/m3 olan farklı bir malzeme kırıldığında kapasitenin de aynı oranda düşeceği unutulmamalıdır ya da tam tersinin olacağını hatırlamakta fayda vardır.
Çeneli Kırıcıların kapasitesi genel olarak aşağıdaki parametrelere bağlıdır; 𝑄=𝑓(𝑊,𝐿,𝑂𝑆𝑆,𝐶𝑆𝑆,𝑇,𝑛,𝜃,𝑘)
W: Kırıcının Ağız genişliği
L: Kırıcının Ağız Uzunluğu
OSS: Kırıcının maksimum açıklığı
CSS: Kırıcının minimum açıklığı
T: Kırıcının Hareket Miktarı (Throw/Stroke)
n: Kırıcının devir sayısı
𝜃: Kırıcının Kavrama açısı
K: Malzeme ve Kırıcıya özgü faktörlerin değerlendirilmesi sonucunda tayin edilen çarpan faktörü
Çeneli kırıcılar için tasarım parametrelerine bağlı olarak kapasitenin maksimum olduğu ve teorik olarak hesaplanan bir kritik devir sayısı vardır ve aşağıdaki formüllerle hesaplanabilir;
A. Kritik Devir Sayısı-1
Hareket miktarı ve kavrama açısına bağlı kritik devir sayısı formülü;
𝑛𝑐=66,6√𝑇𝑡𝑎𝑛𝜃=√66,62.𝑡𝑎𝑛𝜃𝑇
T – Çene Hareket Miktarı -metre
𝜃 – Sabit ve Hareketli çeneler arasındaki kavrama açısı -° derece
Formülden de anlaşılacağı gibi çeneli kırıcılarda kritik devir sayısı kavrama açısına (𝜃) ve kırıcının bir turdaki toplam hareket miktarına (T) bağlıdır. Kavrama açısı arttıkça kritik devir sayısı da artar. Kırıcının hareket miktarıyla (Throw) ise ters orantılıdır ve hareket miktarı (throw) arttıkça kritik devir sayısı azalır.
Kavrama açısı değişirse;
𝜃=20 ° 𝑣𝑒 𝑇=0,04 𝑚 için 𝑛𝑐=200 rpm
𝜃=25 ° 𝑣𝑒 𝑇=0,04 𝑚 için 𝑛𝑐=227 rpm
Hareket Miktarı (Throw) değişirse;
𝜃=20 ° 𝑣𝑒 𝑇=0,04 𝑚 için 𝑛𝑐=200 rpm
𝜃=20° ° 𝑣𝑒 𝑇=0,05 𝑚 için 𝑛𝑐~180 rpm
B. Kritik Devir Sayısı-2
Hareket miktarı ve indirgeme oranına bağlı bir kritik devir sayısı formülü;
𝑛𝑐=47√𝑇√𝑅−1𝑅 =47√𝑇.√1−1𝑅
Kavrama açısı ise geometrik olarak düşünüldüğünde indirgeme oranıyla doğrudan bağımlı bir parametredir.
Son formülü değerlendirirsek eğer; çeneli kırıcılarda indirgeme oranı sabit kabul edilirse hareket miktarı (T) arttıkça kritik devir sayısı düşmektedir. Hareket miktarı (T) ise yine kırıcıya ait tasarım özelliklerindendir ve sabit kaldığını düşünmek yanlış olmaz. Bu durumda indirgeme oranını arttırmak için devir sayısını artırmak gerekecektir. Çeneli kırıcılarda kritik devir sayısını belirleyen en önemli etken kırıcı çenenin hareket miktarıdır (Throw).
Kırıcı Kapasitesi:
Literatürde çeneli kırıcıların kapasitelerinin hesaplanması açısından birden fazla formül bulunmaktadır. Aşağıda sadece örnek olması açısından birkaç formül verilmiştir.
Taggart Formülü:
𝑄 (𝑡𝑜𝑛𝑠𝑎𝑎𝑡)=0,6.𝐿(𝑖𝑛ç).𝑂𝑆𝑆(𝑖𝑛ç)
𝑄 (𝑡𝑜𝑛𝑠𝑎𝑎𝑡)=930.𝐿(𝑚).𝑂𝑆𝑆(𝑚)
L: Çeneli Kırıcı Ağzının uzunluğu -metre
OSS: Çeneli Kırıcı Maximum Çıkış ayarı-OSS-metre
Lewenson Formülü:
𝑄(𝑡𝑜𝑛𝑠𝑎𝑎𝑡)=150.𝑛.𝐿.𝑇.𝑑.𝜇.𝛾
n: Kırıcı devir sayısı-(rpm)
L: Hareketli Çenenin Genişliği (Yaklaşık değer olarak Çeneli Kırıcı Ağzının uzunluğu alınabilir.)-m
T: Çeneli kırıcı Hareket miktarı (throw)-m
d: Çıkan ürünün ortalama ölçüsü-m
𝝁: 0,25-0,5 arasındaki yükleme katsayısı (Loading Factor)
𝜸:𝑀𝑎𝑙𝑧𝑒𝑚𝑒𝑛𝑖𝑛 Ö𝑧𝑔ü𝑙 𝐴ğ𝚤𝑟𝑙𝚤ğ𝚤 (ton/m3)
Broman Formülü:
𝑄(𝑚3𝑠𝑎𝑎𝑡)=𝑊.𝑂𝑆𝑆.𝑇.𝑘.60.𝑛𝑡𝑎𝑛𝜃
W: Çeneli Kırıcı Ağzının genişliği-m
OSS: Çeneli Kırıcı Maximum çıkış ayarı-m
T: Çeneli kırıcı Hareket miktarı (throw)-m
k: 1,5-2,5 arasında sabit katsayı
n: Çeneli kırıcı devri-rpm
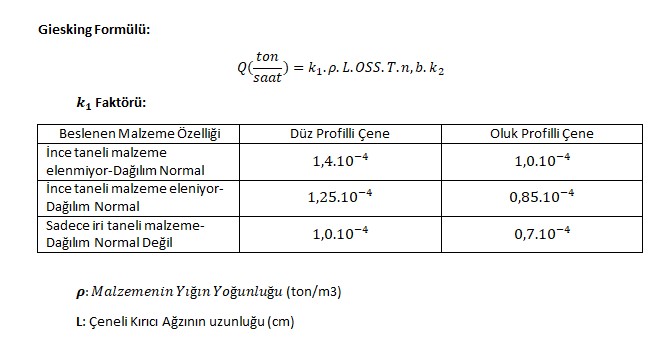
𝝆:𝑀𝑎𝑙𝑧𝑒𝑚𝑒𝑛𝑖𝑛 𝑌𝚤ğ𝚤𝑛 𝑌𝑜ğ𝑢𝑛𝑙𝑢ğ𝑢 (ton/m3)
L: Çeneli Kırıcı Ağzının uzunluğu (cm)
OSS: Çeneli Kırıcı Maximum çıkış ayarı (cm)
T: Çeneli kırıcı Hareket miktarı (throw)-m
n: Kırıcı devir sayısı-(rpm)
b : Kavrama açısı düzeltme faktörü

𝒌𝟐 Faktörü: Teorik ve pratik kapasite arasındaki oran : 0,8-0,9 aralığında alınabilir.
Yukarıdakilere benzer formüllerden literatürde daha da bulabilmek mümkündür.
Hemen hemen tüm formüllerin içerisinde sonuca mutlaka etki eden sübjektif parametrelere rastlamak mümkündür. O yüzden belirli bir formül hesabından sonra sonuca dikkatli yaklaşmak ve yorumlamakta fayda vardır.
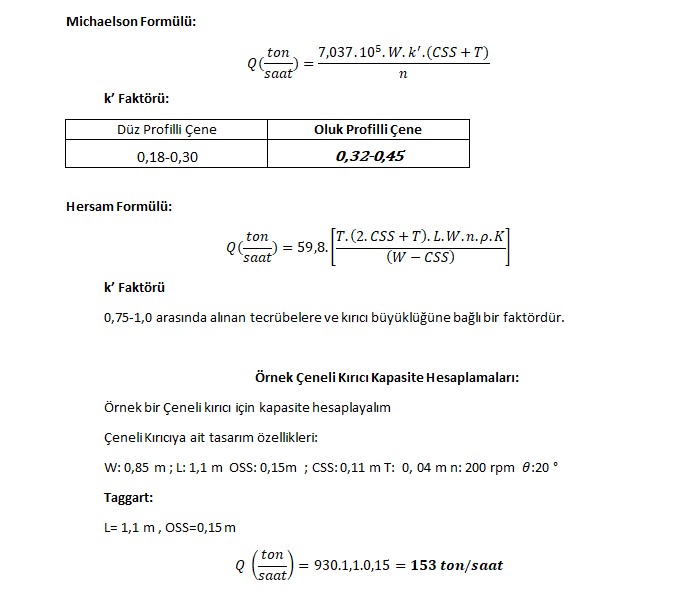
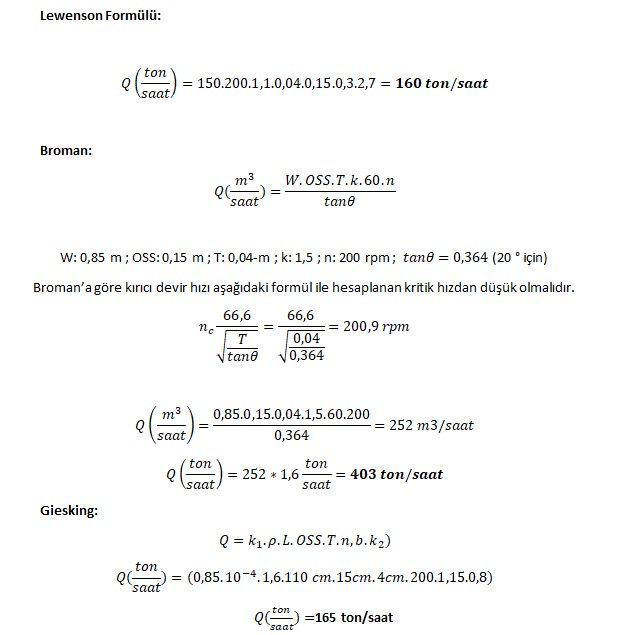
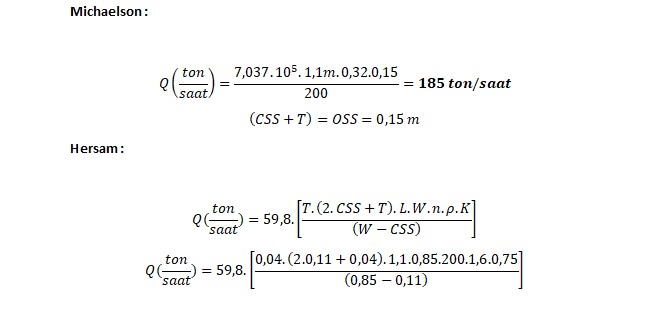
𝑄(𝑡𝑜𝑛𝑠𝑎𝑎𝑡)=59,8.[2,334(0,74)]=𝟏𝟖𝟖 𝒕𝒐𝒏/𝒔𝒂𝒂𝒕
Örneklerden görüldüğü üzere Broman formülüne göre hesapladığımız kapasite değeri diğerlerine nazaran oldukça yüksek çıkmaktadır. Diğer formüllerde ise birbirine yakın değerler bulunmuştur. Hangi formül kullanılırsa kullanılsın, hesaplamada bulunan kişiye bağlı faktörler, kırıcıya ve malzemeye bağlı değişkenlikler nedeniyle tek bir sonuç elde etmek güçtür. Pratik tecrübelere göre elde edilen etkin kapasitelerle hesaplanan değerleri mutlaka kıyaslamak gereklidir.
Kırıcı Motor Gücü:
Kırıcının motor gücü için de aynı kapasite hesabında olduğu gibi literatürde farklı yöntemler ve hesaplamalar yapılmıştır.
Viard Formülü:
P=155.L.W (HP)
L: Çene Ağzı Uzunluğu-m
W: Çene ağzı genişliği-m
1100x850 mm Çeneli kırıcı için :
P=155.1,1.0,85=145 HP
Lewenson Formülü:
𝑷 (𝑯𝑷)=𝒏.𝑳.(𝑫𝟐−𝒅𝟐)𝟎,𝟑𝟒
D: Ortalama beslenen malzeme büyüklüğü-m
d: Ortalama kırılan malzeme büyüklüğü-m
1100x850 mm Çeneli kırıcı için D~500 mm ve d~110 mm olarak alınırsa;
𝑷 (𝑯𝑷)=𝟐𝟎𝟎.𝟏,𝟏.(𝟎,𝟓𝟐−𝟎,𝟏𝟑𝟐)𝟎,𝟑𝟒=𝟏𝟓𝟏 𝑯𝑷
Çeneli kırıcılar için motor gücünü hesaplamalardan %15-20 kadar daha büyük seçilmesi uygun olacaktır.
Rose &English Formülü:
𝑷 (𝒌𝑾𝒉)=𝟏𝟎.𝑾𝒊.𝑸.[𝟏√𝟕𝟎𝟎.𝟎𝟎𝟎.𝑶𝑺𝑺−𝟏√𝟔𝟑𝟎.𝟎𝟎𝟎.𝑾]
𝑊𝑖.:𝐾𝚤𝑟𝚤𝑙𝑎𝑛 𝑀𝑎𝑙𝑧𝑒𝑚𝑒𝑦𝑒 𝑎𝑖𝑡 𝐵𝑜𝑛𝑑 𝑊𝑜𝑟𝑘 İ𝑛𝑑𝑒𝑘𝑠𝑖 (Kalker için 13-14 kw/t alınabilir.)
𝑄:𝐾𝚤𝑟𝚤𝑐𝚤 𝑘𝑎𝑝𝑎𝑠𝑖𝑡𝑒𝑠𝑖−𝑡𝑜𝑛
𝑂𝑆𝑆:𝐾𝚤𝑟𝚤𝑐𝚤 𝑎𝑦𝑎𝑟𝚤 𝑚𝑎𝑘𝑠𝑖𝑚𝑢𝑚 𝑎ç𝚤𝑘𝑙𝚤ğ𝚤−𝑚
𝑊:𝐾𝚤𝑟𝚤𝑐𝚤 𝐴ğ𝑧𝚤 𝐺𝑒𝑛𝑖ş𝑙𝑖ğ𝑖−𝑚
𝑃 (𝑘𝑊ℎ)=10.14.250.[1√700.000.0,15−1√630.000.0,85]=61 𝑘𝑊/ℎ
Bu formül kırılan malzeme cinsine, indirgeme oranı (R) ve kapasiteye göre ortalama motor gücünü vermektedir. Makine tasarımında seçilmesi gereken motor güçleri hesaplanandan daha yukarıda olacaktır.
Kırıcı Çıkış Ürün Dağılımı:
Çeneli kırıcıların çalışma mekanizmaları nedeniyle (Her çalışma periyodu süresince kırıcı çıkış açıklığı minimum ve maksimum değerler arasında açılıp kapanır) çıkışından alınan ürün ebatlarının %65-70 inin ayar mesafesinden küçük olduğunu düşünebiliriz.
Örnek olarak kırıcı çıkış ayarının kapalı konumunun 130 mm olarak ayarlandığını düşünürsek eğer, bu ayardaki bir çeneli kırıcının üretmiş olduğu ürünlerin %65-70 inin 130 mm’den daha küçük olduğunu söyleyebiliriz.
Çeneli kırıcıdan çıkan ürünlerin en büyük ebatları için ise kesin olmamakla birlikte (Beslenen malzemenin şekil özelliklerine de bağlıdır) kapalı ayar konumunun yaklaşık 1,5 katını almak uygundur.
MTM tarafından üretilen Primer ve Sekonder kırma aşamalarında kullanılan çeneli kırıcılar, teknik değerleri ve örnek bir ürün dağılım grafiği aşağıdaki verilmiştir.
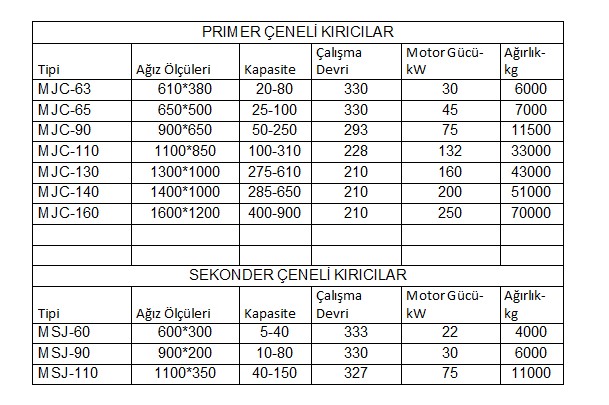
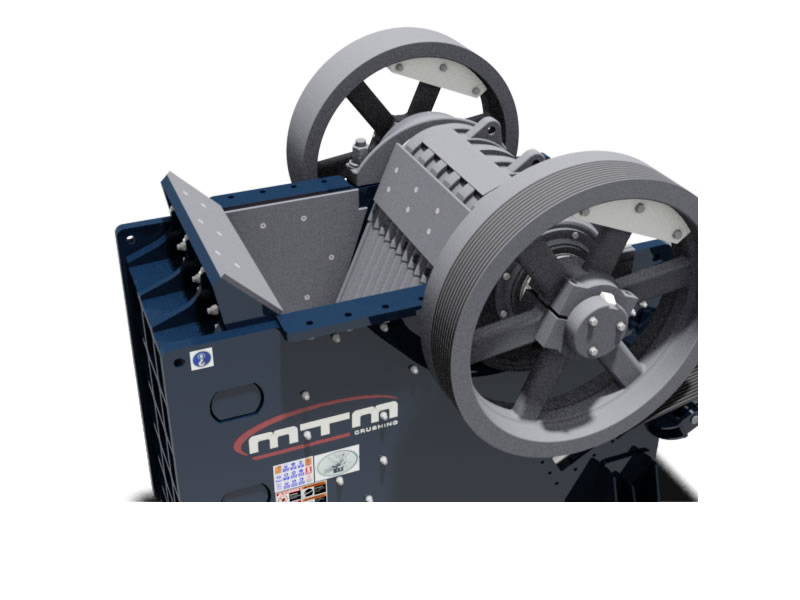
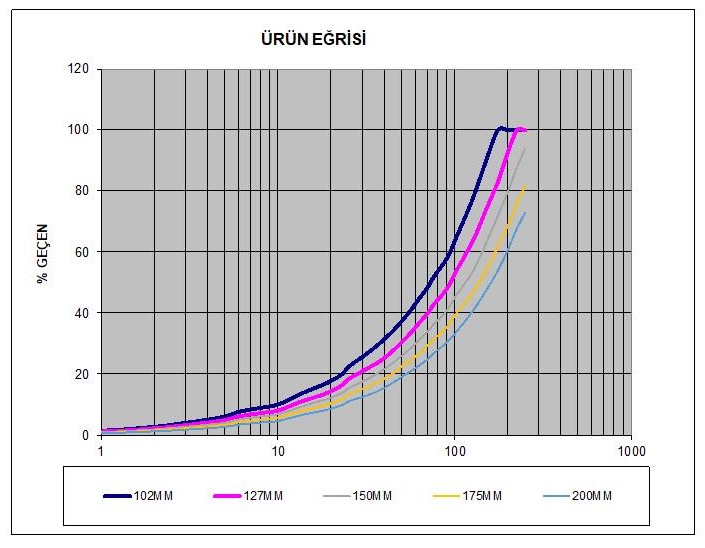